Hitting quality targets for nuclear projects
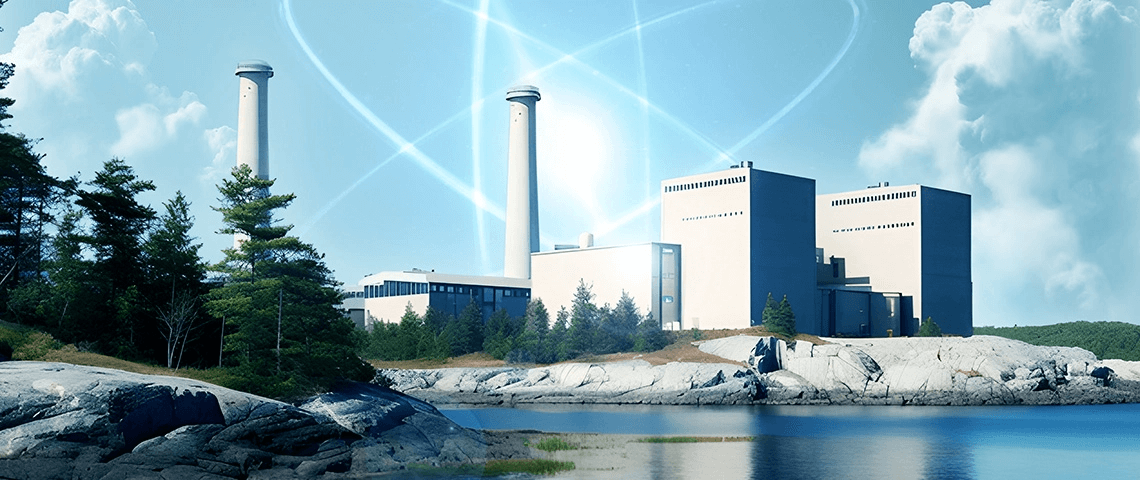
With nuclear power generational having a resurgence, it’s worth reflecting on the role of stainless steel in the industry. Andy Backhouse, Lead Technical Manager at Outokumpu, explains how stainless steel for nuclear projects differs from the material in other sectors.
When the International Energy Agency published its World Energy Outlook published in October 2022, it made headlines. For the first time in history, the organisation has forecast that fossil fuel consumption will peak during the 2020s – a development that has been triggered by the energy crisis.
The report envisages growing use of nuclear energy alongside renewables. This will create new opportunities for the sector. It’s likely that we’ll see accelerated development of traditional large-scale reactors, as well as small modular reactors (SMRs) and very small or micro-modular technology.
What all types of nuclear reactor have in common is that they often use stainless steel as a material for pipework, tanks, vessels, pools, filters and waste containers. Stainless steel provides the corrosion resistance that ensures a long lifetime with little or no maintenance required – and therefore is valuable in managing health, safety and environmental risk. We typically supply it in the form of quarto plate in thicknesses upwards of 4mm for heavy duty applications, as well as thinner sheets and coils for liners and tube manufactured for pipework.
“
It’s likely that we’ll see accelerated development of traditional large-scale reactors, as well as small modular reactors (SMRs) and very small or micro-modular technology.
When specifying stainless steel for nuclear projects, a reduced level of cobalt is one of the most important factors. Even though cobalt is often not considered as an alloying element, it can still appear as a trace element in stainless steels, and particularly ones that contain nickel. This is because most nickel deposits naturally contain trace amounts of cobalt.
This creates a major challenge for nuclear power station operators as cobalt transforms into a highly radioactive isotope when it is exposed to radiation. As a result, reactor infrastructure becomes more radioactive over time, creating a risk for maintenance technicians.
To minimize this effect, nuclear design engineers typically specify a low-cobalt stainless steel. It’s possible to produce this by sourcing nickel that has been mined from deposits that naturally have very low cobalt content.
The other factor that is unique for nuclear projects is that they have extremely stringent requirements for quality assurance and testing such as the RCC-M standard. We typically follow a standard process to produce all our stainless steel products in the right grade at the right time and in the correct quantity.
However, the bar is much higher for the nuclear industry. The plant operator and its engineering design contractor apply stringent quality requirements. The first step in meeting these is to interpret the technical requirements and put in place additional project management and production management to ensure that the requirements are covered.
“
Having supplied materials for nuclear power stations around the world since the 1960s, we have developed the project management techniques to meet these requirements for each project, down to the very finest details.
During production, we may also need to host customers or representatives from a third-party regulator or certification authority to join us at the mill and witness production. In addition, we need to allow for extensive quality testing and provide the capability for the customer or their representative to carry out their own testing. We also establish systems to guarantee complete traceability at every stage.
Having supplied materials for nuclear power stations around the world since the 1960s, we have developed the project management techniques to meet these requirements for each project, down to the very finest details.
Sustainability is growing in importance for all construction projects and project developers are striving to minimize the embodied carbon dioxide in construction materials of buildings and infrastructure. At Outokumpu, our carbon footprint is 70% lower than the global average for the stainless steel industry as we have invested in energy saving technology and use renewable energy to power our plants.
Technology for large-scale reactors is well-established and typically, water and steam are used to generate power and provide cooling. Engineers follow sets of design principles and standards that are widely recognized. Projects are often delivered over the course of many years and we typically work most closely with fabrication contractors.
When selecting a stainless steel for a large power plant, engineers are often guided by a list of approved materials that have passed a rigorous evaluation process. These typically include variations of the well-established grades of 304L and 316L. Meanwhile super duplex grades SDX 2507 and the super austenitic grade Ultra 254 SMO can be chosen for applications where higher levels of corrosion resistance is needed, for example in seawater intake and handling systems at coastal sites.
The nuclear industry is developing with ideas to modularize and standardize designs to allow faster build, whilst keeping costs down and reducing financial risk. Many companies are developing small and micro reactor technologies, some of which are based on conventional technologies, while others strive for commercial implementation of experimental or novel techniques. At the smallest end of the scale, an array of companies are developing micro modular nuclear reactor technology. Such reactors will open up a new area for nuclear applications in off-grid power supply, for example cutting reliance on diesel for extremely remote communities.
“
Ultimately, whichever grade or product is selected, every nuclear operator needs a high quality stainless steel produced to the highest standards of quality and traceability.
Some of these projects are exploring the potential of alternative reactor coolant fluids such as high temperature gases or molten salts. Striving for long term zero maintenance in remote locations puts greater emphasis on selecting appropriate materials both for reactor internals and balance of plant components. As a result, engineers are considering a wider range of alloys to provide the required performance for, process equipment and structural components etc. Outokumpu’s materials experts have long experience in materials selection in stainless steel are able to assist with these questions.
Ultimately, whichever grade or product is selected, every nuclear operator needs a high quality stainless steel produced to the highest standards of quality and traceability. Therefore, it’s worth choosing a supplier with a history of success in the industry.
Outokumpu has a wealth of experience in supplying the nuclear industry with stainless steel. Fill in your details to receive a detailed guide covering our Core, Supra, Forta and Ultra range stainless steels as well as our industry-leading expertise and support for nuclear projects.
Best wishes,
Outokumpu team
This might happen because of Ghostery or adblocker. Try disabling them and refresh the page.